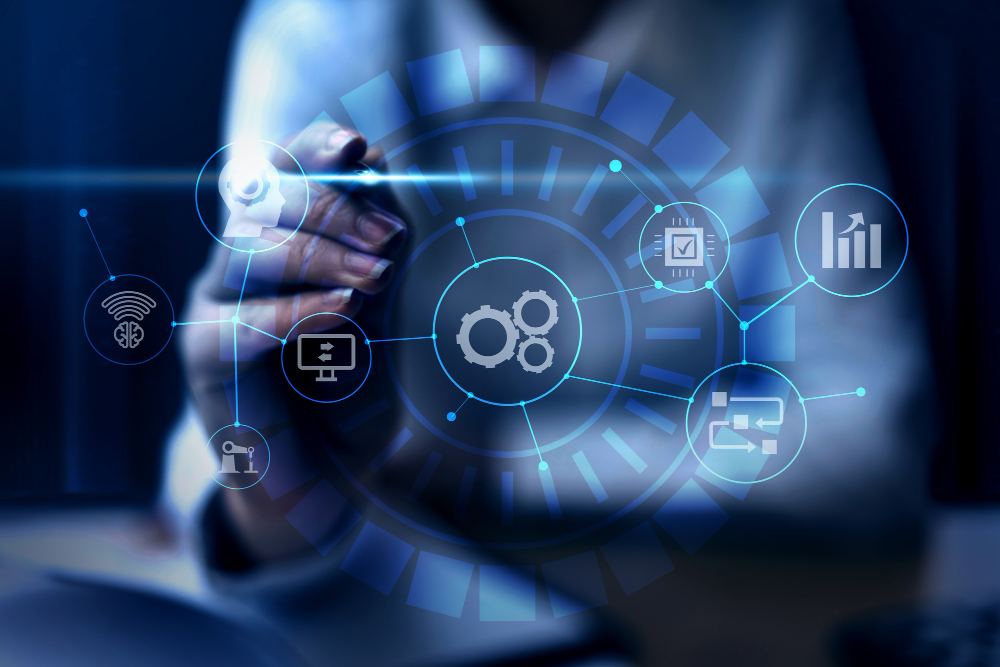
Todos sabem que os pensadores Lean e TI (Departamento de Tecnologia de Informação) têm uma guerra aberta travada. Defensores do Lean reclamam que o TI é lento para vir a mesa Lean (assim falando) e as tradicionais soluções de TI são as maiores pedras no caminho para implementar a Cadeia de Suprimentos Lean. O desprezo do mais enxuto dos pensadores Lean para o TI é demonstrado pelos botões de “SEM MRP.”
Todos nós sabemos que os Processos vêm antes do Sistema. Mas nós sabemos o que os processos de Distribuição Lean serão? Podemos dizer que tipo de Sistema será necessário para suportar estes processos? Vamos explorar algumas destas possibilidades:
Comunicações: Como os sinais de puxada substituem a tradicional liberação de materiais pelo MRP e a empresa aproveita a rede de suprimentos direcionada pela demanda; o reconhecimento instantâneo de ponta-a-ponta será essencial para lead times de reposição curtos. Alguém pode usar cartões em um sistema de transporte de circuito fechado com múltiplas entregas diárias, mas cartões não viajariam bem. TI precisará coletar a demanda, organizar de acordo com a rota de reposição e enviar tudo pela Cadeia de Suprimentos Lean.
Claro que isto é uma notícia velha; isto é básico, mas o que você faz com os dados é que faz disto uma Cadeia de Suprimentos Lean.
Custos de Transação / Estrutura: A maior barreira para utilizar demandas mais frequentes é o custo de transação para desenvolver e processar Requisições de Compra (RC), incluindo a verificação do material com as RC´s no recebimento. A chave que conduz para grandes quantidades de compras na fórmula para Quantidade Econômica na Requisição é o custo das Requisições. Um local especial está reservado para aquelas pobres almas no recebimento com a tarefa difícil de tentar identificar o que acontece na chegada versus o registro no sistema. Não é de admirar que Compras seja relutante para criar mais uma RC. O Guru Lean está pedindo RC´s para 1 unidade. Tremo só de pensar o que ocorreria na Contabilidade.
TI virá conduzindo os custos das Requisições para próximo de zero. As tradicionais RC´s sairão, sendo substituídas com RC como eventos incluindo os Cartões Kanban, diariamente ou com lançamentos várias vezes por dia. A RC não será mais um evento discreto, mas encarnará uma relação e estabelecerá as condições para aceitar os lançamentos. As atribuições de Preços serão um conjunto de dados compartilhados entre fornecedor e cliente, as faturas serão criadas mediante o recibo do Kanban e o pagamento será gerado pelo Recebimento com base no tempo preestabelecido, sem uma fatura. Parecerá tão fácil, que a maioria de nós se perguntará por que levou tanto tempo.
Planejamento de Kanban e Manutenção: Mesmo os defensores de Lean estão implorando por uma solução para os Cartões Kanban e Manutenção. Qualquer um que calculou os tamanhos de circuito de Kanban imprimiu e desdobrou cartões sabe que isto não é uma tarefa fácil. E aqueles que tiveram a infelicidade de ficar sem um item de Kanban podem atestar a sensação de que você realmente não sabe o porquê. A criação de um sistema Kanban para um centro de distribuição com dezenas de milhares de itens faz com que uma fábrica de montagem com alguns milhares parecer moleza.
As soluções de TI não somente determinarão o número de Kanbans, mas também monitorarão as operações e determinarão quando o número de Kanbans deverá ser ajustado. Reduzir a quantidade de materiais quando apropriado será onde TI pode ser aproveitado em atingir novos níveis em Lean. Os sistemas também transmitirão Kanbans em formato apropriado para aqueles que não estão no circuito e colocarão um fim ao trabalho de checagem e roteamento nas docas. Para todos aqueles que estão buscando o formato padrão para o Kanban, em pouco tempo ele não vai ou não precisará existir.
Planejamento e Controle de Operações: Mr. F. Cho quando era o Presidente da Toyota Motor Corporation disse uma vez que o Lean na planta de montagem era fácil se comparado a um Centro de Distribuição. A planta tem uma esteira acorrentada que apresenta um trabalho a cada 60 segundos; o operador fica impedido de adiantar ou atrasar o trabalho. No Centro de Distribuição não há um ritmo estabelecido. Somente perguntem se eles estão adiantados ou atrasados. Para um homem, eles dirão que estão atrasados ou estarão atrasados se eles não coletarem o mais rápido possível. Mesmo nos armazéns automatizados, não há nenhum ritmo. Parece que a automação suporta cada vez maiores lotes de coleta otimizando a coleta, enquanto piora na separação e embalagem. (Para todos os Taylorianos que acreditam que reduzir ondas é a forma de serem mais eficientes; nós perguntamos: por que não uma onda por dia ou uma por semana? Por que não uma onda por mês?).
TI suportará a Cadeia de Suprimentos Lean por melhorias dramáticas nas operações do Centro de Distribuição permitindo requisições e reabastecimentos mais frequentes. O que nós esperamos é que as soluções de sistemas analisem o nível de trabalho do dia, estabelecendo um número de coletas e recebimentos de lotes requisitados para manter os objetivos de desempenho, estabelecendo o tempo TAKT de acordo com a janela de trabalho normal, determinando os números de operadores de acordo com os tempos de ciclo dos lotes do trabalho padrão e avisar aos supervisores se a hora-extra será necessária. Quando os operadores estiverem disponíveis, serão dados aos supervisores uma seleção de inventário, limpeza ou outros tipos de lotes para o sistema expedir. Operadores serão reservados para projetos de resolução de problemas de acordo com os objetivos do Centro de Distribuição. Toda vez que o sistema criar um plano, ele automaticamente nivelará ondas de coleta versus separação e embalagem baseado no conteúdo do trabalho.
Esperar isto não para com o desenvolvimento do plano. O sistema também monitorará continuamente o progresso e registrará os problemas para a futura resolução de problema e informará a supervisão quando um inventário for necessário. Operadores serão transferidos de uma atividade para outra sem interrupções, com o sistema controlando o tempo de acordo com o TAKT calculado e atribuição do grupo de tarefas. Se um trabalho adicional for recebido, o sistema analisará o trabalho e fará o cálculo apropriado para desenvolver um novo plano, o qual será executado sem intervenções. Os grupos de tarefas revisados simplesmente fluirão aos operadores ou se necessário para alocação de mão-de-obra.
Na nova solução de TI, quando o Gerente de CD (Centro de Distribuição) for perguntado: ”Como está indo?” Ele responderá: “Ótimo, o plano prevê embarcarmos 100 caixas na primeira hora e nós já embarcamos 99. Espere! A 100ª acabou de sair. Por agora normalmente temos 14 lotes que não foram completos conforme o plano, normalmente 10 levam menos tempo e 4 levam mais. Hoje nós apenas temos 9 – 7 adiantados, e 2 atrasados. O Time de Kaizen está realmente fazendo algum progresso. Nós acabamos de receber o resto do reabastecimento para a requisição que estava feita 10 dias atrás, só 2 dias mais que o tempo de trânsito.”
Como vocês podem ver, TI será uma parte integral proporcionando: mídia para comunicar a demanda, desenvolvendo processos que reduzem estrutura e melhorias operacionais. Tradicionalmente olhamos o desempenho de produtividade do passado como uma maneira para julgar como estamos indo. Nós realmente não sabemos como mudar o número que foi reportado. Tempo não atribuído e perda de tempo por problemas que foram encontrados são os maiores obstáculos na melhoria de produtividade.
Nós achamos que as organizações precisarão se afastar da tradicional resolução de problema enquanto elas movem para o ambiente onde o ritmo está estabelecido para cumprir os requisitos dos clientes instantaneamente. O sistema coletará os dados-chaves e apresentá-los-á em uma forma que os operadores instantaneamente terão o apropriado entendimento da condição atual. A capacidade de resolução de problema de todos será elevada pela disponibilidade dos dados que são suportados pelos sistemas que serão desenvolvidos.
Nós estamos empolgados com o futuro e aguardamos seus comentários. Por favor, enviem um email para perguntas ou comentários para Dan Mulloy: d.mulloy@br.honsha.org.
Dan Mulloy
A carreira de Dan já dura mais de 30 anos com a General Motors e a Toyota Motors, aprendendo e aplicando os princípios do Sistema Toyota de Produção em uma variedade de ambientes de fabricação, engenharia, logística e distribuição. O seu conhecimento profundo da cadeia de suprimentos de fabricantes de veículos, estratégia de fabricação e atividades de compras fornecem uma perspectiva detalhada única sobre os principais atributos e diferenças de cada um.
Ganhou experiência prática sobre a cadeia de suprimentos lean quando trabalhou diretamente com os especialistas da Toyota como Gerente de projetos, transformando a cadeia de suprimentos de peças de serviço, da Toyota NA, através do TPS/Lean. O projeto incluiu a reengenharia das peças de reposição de layout e a transformação completa das operações diárias de recebimento/coleta. Este projeto foi citado em “Pensamento Lean” (Thinking Lean) de autoria de Jim Womack e Dan Jones.
Dan estava mergulhado na metodologia da Toyota, enquanto parte da equipe de Planejamento estratégico, e ganhou conhecimento prático da Toyota Kaizen ao treinar facilitadores que impulsionaram os projetos de melhoria ao longo dos centros de distribuição de peças. Nesta tarefa, foi responsável pelo desenvolvimento d a estratégia geral de Kaizen, incluindo critérios de avaliação e uma celebração anual. Na Toyota, conduziu workshops de Hoshin Kanri e treinamento em A3.