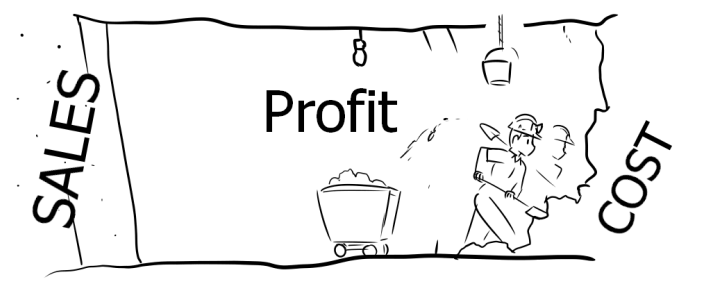
Muito se tem falado sobre os benefícios de implantação do Lean, mas uma pergunta é recorrente: o Lean é uma despesa ou um investimento? E ao tentarmos responder essa pergunta, muitas outras surgem: quais serão os recursos necessários para a implantação de um programa Lean? Quantas pessoas e materiais? Qual a área ou infraestrutura necessária? Quantos outros meios deverão ser mobilizados?
Decidir antes de prosseguir…
Antes de responder todas essas perguntas, temos que nos questionar sobre o quanto estamos dispostos a investir. Sim, pois aqui não estamos tratando de uma despesa ou um custo de implantação, mas sim um investimento. A grande diferença é que no conceito de investimento espera-se um retorno ou benefício sobre o valor investido, enquanto na despesa é algo necessário para o seu negócio. Esse investimento vai exigir uma dedicação enorme de suas equipes, como várias horas de treinamento, simulações, Genba Walk, apoio às equipes, orientação da liderança, entre outros atividades. Uma consultoria pode indicar o caminho das pedras, mas quem cruzará o rio será você.
Um dos desafios de qualquer gestor é a entrega dos melhores resultados com a máxima eficiência. Esse desafio fica ainda mais complexo quanto falamos de tamanho do investimento pois ele deve ser justificado pelos ganhos associados à implantação. Embora existam ganhos gigantescos em agilidade, decisão, capacitação das equipes e engajamento na implantação do programa Lean, as organizações ainda sentem uma grande dificuldade na mensuração dos eventuais ganhos financeiros, uma vez que o conceito básico é produzir mais com menos recursos. Eis então que um esclarecimento se faz necessário: precisamos produzir mais para atender a demanda?
Podemos implementar mudanças drásticas aumentando a produção, mas sem a demanda correspondente, caímos na armadilha de sermos cada vez mais eficiente tendo o estoque como destino da produção. Com a demanda constante, a saída será produzir a mesma quantidade de maneira mais eficiente, aplicando o conceito do Takt-time: produzir de acordo com a demanda do cliente.
Mas como saber se estamos produzindo conforme a demanda? E como calcular o retorno?
Umas das formas é identificar se o seu cliente está sendo atendido através das respostas de algumas perguntas, como: qual a quantidade de pedidos que não foram atendidos? Quantos dias de atraso? Qual quantidade e quais produtos em atraso?
Quando entendemos que há uma demanda não atendida e que o aumento da produção gera mais vendas realizadas, transformamos os ganhos da primeira decisão de vendas adicionais em retorno esperado do investimento no programa Lean, e para calcular lucratividade, aplicamos o lucro operacional ou EBTIDA (Earnings before interest, taxes, depreciation and amortization em inglês), conforme a orientação da organização.
Taiichi Ohno já nos avisava do caso oposto, onde há oferta mas não há procura suficiente, em seu livro “O Sistema Toyota de Produção: Além da Produção em Larga Escala”:
"Não há desperdício mais terrível em uma empresa do que a superprodução."
A produção além do necessário ou superprodução faz do estoque o destino do excedente e o cálculo do retorno da aplicação do Lean fica claro ao vermos a redução de estoques e a disponibilidade de caixa imediato que não foi imobilizado nos custos de produção além da demanda.
No caso da demanda constante, onde temos que manter o foco em custos, o primeiro passo é entender a estrutura de custos da empresa e, a partir daí, traduzir os ganhos Lean em ganhos financeiros. O caminho natural é a análise dos 7 desperdícios:
1. Estoque: a partir da sua frequência de entrega verificar quando possui de estoque. A redução do estoque traduz-se imediatamente em fluxo de caixa disponível. Outro aspecto é a quantidade de embalagens, depósitos, pessoal, equipamentos de movimentação, entre outros, necessários antes e depois.
2. Movimentação: a redução da movimentação irá se mostrar em otimização de mão de obra ou redução de horas extras.
3. Transporte: redução dos fretes, despesas com veículos, rebocadores, empilhadeiras ou operadores necessários para levar produtos de um lugar para outro.
4. Refugo: redução dos retrabalhos ou peças refugadas surtirá efeito na quantidade de peças boas entregues para seu cliente ou próximo processo.
5. Processamento: como no refugo, a eliminação ou redução se traduzirá numa quantidade maior de peças boas ao se evitar o acúmulo de horas que não agregam valor ao cliente.
6. Espera: redução de mão de obra ou horas extras uma vez que o tempo será melhor aproveitado. Também poderá se traduzir em maiores quantidades.
7. Super produção: redução de todos os gastos de fabricação, incluindo materiais uma vez que produzirá somente de acordo com a demanda.
(Clique aqui para saber mais como enxergar desperdícios)
Os aumentos de produção mencionados serão transformados em vendas ou custo menor por peça, já que aumentará a produção por homem/hora. As pessoas retiradas do processo são alocadas para efetuar mais kaizens, potencializando as melhorias.
A redução dos 7 desperdícios é identificada principalmente através do Genchi Genbutsu (verificar os fatos onde eles ocorrem), utilizando o 5S para facilitar a visualização e aplicando os conceitos como Trabalho Padronizado, Pokayoke, Jidoka, Kanban, JIT, Takt Time, Fluxo Contínuo, SMED, Problem Solving, FMDS, MFV, entre outros. Um conceito aplicado isoladamente não tornará a organização Lean, mas será um passo na mudança de cultura. A visão de uma caixa de ferramentas é inadequada, uma vez que podemos optar por não utilizar uma ferramenta ou utilizar a ferramenta errada.
Outros ganhos potenciais do Lean adicionais aos já citados são também: a redução de investimento em compras ou aluguéis de equipamentos pois há maior disponibilidade destes (fluxo de caixa) e; a redução de despesa com área, como aluguéis de galpões, tendas e armazéns.
Uma vez esclarecido, a conclusão que chegamos é que qualquer gasto com implantação de Lean tem que passar por uma análise de retorno de investimento, uma vez que uma implantação com metodologia, técnica e conhecimento, levará a um ganho financeiro. O investimento é temporário, mas o ganho é permanente.
José C. Farias, CFO do Honsha.ORG, economista com MBA em Gestão de Negócios, com mais de 26 anos de atuação na Toyota do Brasil, Japão, Argentina e Venezuela, atuou em Planejamento Estratégico, Gestor das áreas de Finanças Corporativas, Recursos Humanos, Treinamentos, Administração, Segurança Industrial, Meio Ambiente e Planejamento e Controle da Produção, certificado como instrutor de TBP (Toyota Business Practice) e OJD (On the Job Development) pela Toyota Motor Corporation.
Quer saber mais sobre o Honsha.ORG? Conheça o nosso site.
Clique aqui para conhecer outros artigos do Honsha.ORG.
Siga-nos no YouTube.