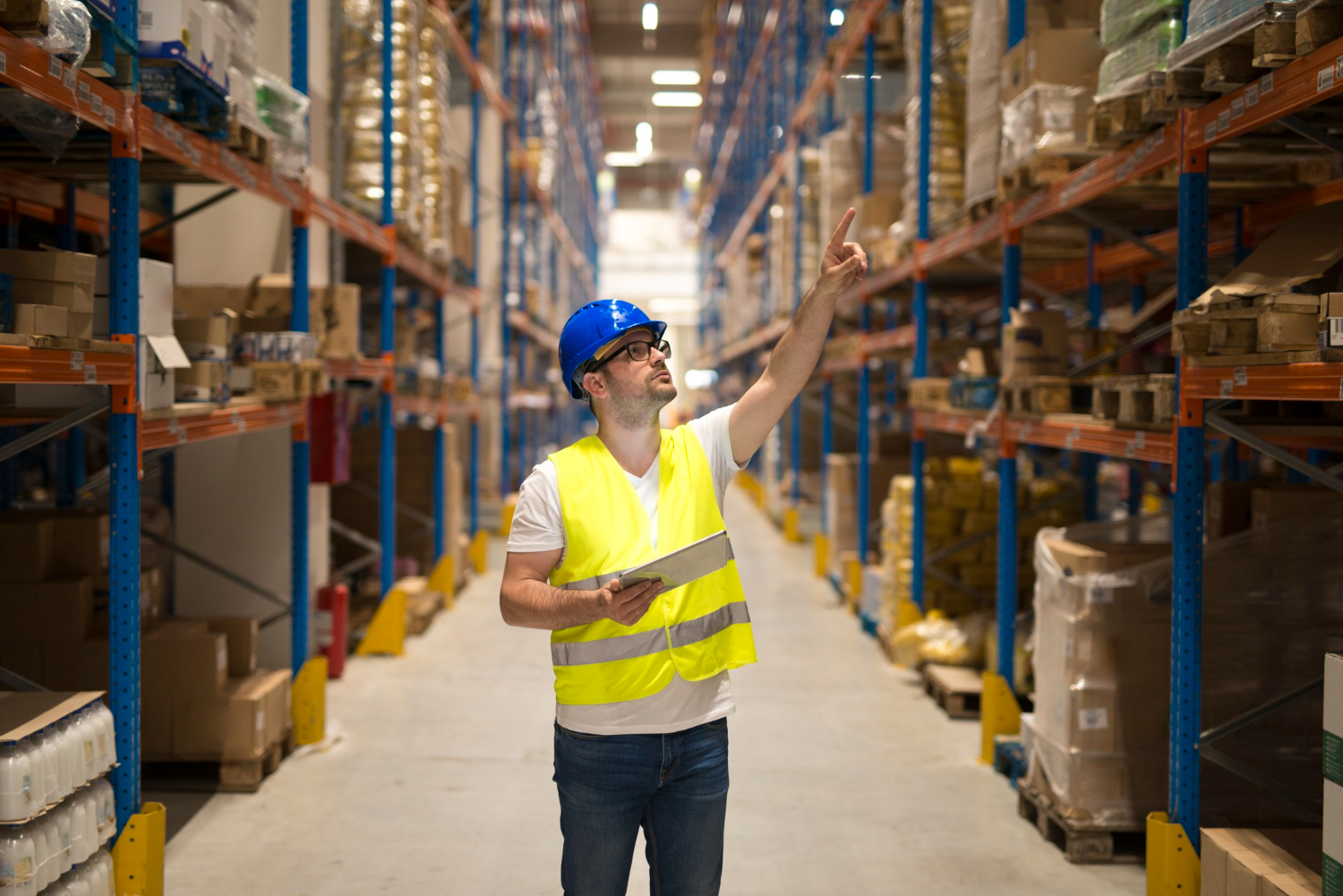
Esta é uma pergunta muito feliz feita por um aluno durante o atendimento em um cliente.
Estávamos repassando os fundamentos do Lean para uma turma de alunos – os Sete Desperdícios.
Explicamos os Sete Desperdícios, o motivo pelo qual o HONSHA.org trabalha com os sete, e não oito (ou mais), etc., e em seguida entramos na explicação do Diagrama de Trabalho Padronizado e os elementos que o compõem.
Diagrama de Trabalho Padronizado (ou diagrama de espaguete) é um dos elementos que compõem o Trabalho Padronizado. Ele descreve graficamente como o trabalho é executado naquele processo observado. Contém informações de elementos que compõem o processo (máquinas, equipamentos, estoque padrão em processo) bem como a movimentação do colaborador para executá-lo (relacionado com a folha de combinação de trabalho padronizado), além de pontos de atenção com segurança e qualidade.
Pois quando explicamos como se descreve o estoque padrão em processo, surgiu o debate sobre a importância de fixarmos os conceitos básicos do Toyota Production System.
Qual é o objetivo do Trabalho Padronizado? Não é o de eliminar MURI, MURA e MUDA (sobrecarga, variabilidade e desperdícios)? Estoque não é um dos Sete Desperdícios? Então por que permitimos um estoque padrão em processo? Por que não permitimos um tempo de espera padrão?
É uma delícia quando surgem estas questões.
Se você nunca parou para pensar, pare de continuar lendo o artigo e faça o exercício mental. É muito bom para fixar os conceitos.
Os Sete Desperdícios foram definidos pelo Pai do TPS, Taiichi Ohno, para passar aos seus discípulos o que enxergar e o que eliminar durante o trabalho do dia-a-dia.
São eles:
- Defeito
- Excesso de Processamento
- Espera
- Transporte
- Inventário
- Movimentação
- Excesso de Produção
Quais dos 7 desperdícios estão inversamente relacionados à agregação de valor pelo colaborador? Por que nos atemos a estes desperdícios?
Os desperdícios diretamente relacionados a um colaborador são Espera e Movimentação. Todos os esforços para eliminá-los são justificados. Inclusive o estoque, que permitimos que exista, desde que o mínimo possível.
Isto acontece por exemplo logo após um processo de tratamento térmico. A peça sai quente do processo, e precisa de um tempo de esfriamento, até que a peça atinja uma temperatura segura para manuseio pelo colaborador no processo seguinte. Para que o colaborador do processo seguinte não fique esperando a peça resfriar, permite-se a quantidade de estoque em processo.
Como calcular essa quantidade? Como converter o tempo de resfriamento em quantidade? Tente calcular antes de continuar lendo.
- Meça o tempo de resfriamento.
- Divida esse tempo pelo takt do processo.
Admitir um tempo de espera padrão, para concluir, vejam só, seria padronizar uma não agregação de valor, o que contraria o princípio do TPS – o Sistema Toyota de Produção. Se fizéssemos isto, seríamos assombrados pelo espírito de Taiichi Ohno!
Muito obrigado pela sua leitura! Até a próxima!
Escrito por: Dário Yanagita e Alecsandro Modanez
Dário Yanagita* – d.yanagita@br.honsha.org
*Dário possui 30 anos de experiência em indústria automobilística no Brasil, dos quais 15 anos trabalhando na Toyota do Brasil. Possui especialidade variada, de usinagem, montagem, logística, qualidade e meio ambiente. Implementou linhas de produção Lean, programas Kaizen, geriu planos de desenvolvimento de equipes e transformação Lean em empresas.
Alecsandro Modanez* – a.modanez@br.honsha.org
*Modanez trabalhou mais de 20 anos na Toyota do Brasil. Nesse período, teve a oportunidade de atuar em diversas áreas produtivas e é especialista em Qualidade, Estamparia e Pintura. Ele também foi responsável por treinar equipes internas e de fornecedores em TPS, FMDS, 5S, TJI e Toyota Business Practice. Foi treinado pela Toyota Japão e Toyota do Brasil.