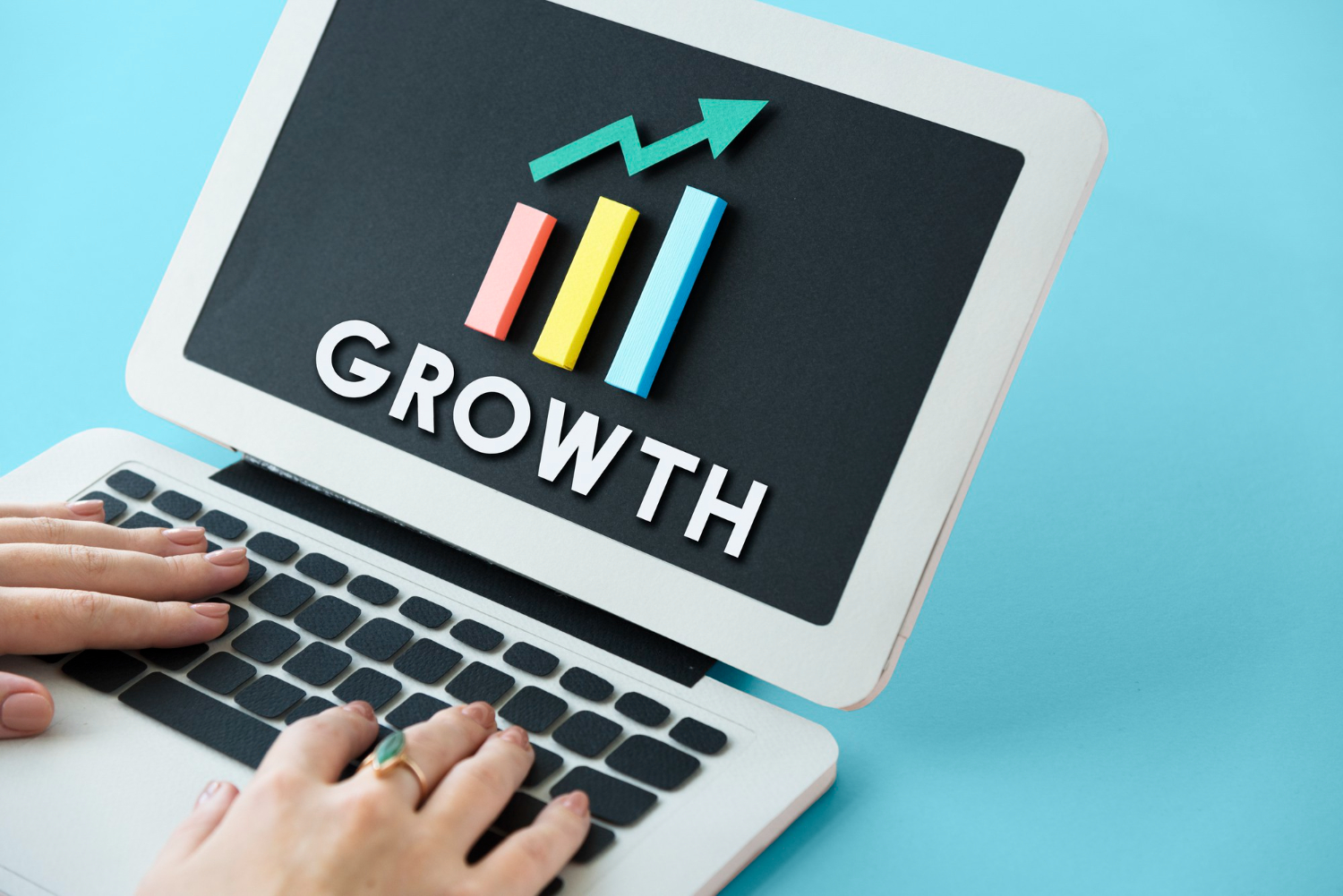
Há dez anos costumava ouvir consultores desaconselharem a implementação do Kanban eletrônico e incentivarem o uso de cartões físicos e quadros, como nos primórdios da criação desse sistema. Evitavam utilizar a tecnologia para não trazer complexidade desnecessária ao chão de fábrica e continuavam focando no Lean, seja desenvolvendo pessoas, capacitando-as na identificação e resolução de problemas ou melhorando os processos continuamente. Aqui notamos um modelo mental interessante: a visão de que tecnologia introduz complexidade, enquanto o Lean está relacionado à simplificação de processos.
Porém, e se a tecnologia ajudasse na simplificação, eliminação de desperdícios e agregação do valor dos processos do cliente? Esse embate teria uma trégua e o Lean e a Tecnologia seriam aliados? É sobre essa cooperação que vamos explorar nesse artigo! Vamos mostrar como os avanços tecnológicos descomplicaram a transformação digital na gestão Lean e compartilhar exemplos que podem incrementar os seus ganhos.
Antes do salto, o primeiro passo…
Lembrar o propósito do Lean e aplicá-lo é o primeiro passo para viabilizar essa aliança. Como sabem, o princípio básico do Lean começa com a agregação de valor ao cliente, ou seja, tudo que não agrega valor é visto como um desperdício pois gera custos, consome tempo e recursos. Não aplicar o Lean é um sério risco de investir em tecnologias automatizando desperdícios.
(clique aqui para saber mais sobre Lean)
Um ganho adicional do Lean é a redução do leadtime de implementação de novas tecnologias pois suas ferramentas, como padrões e sistemas de qualidade na fonte, agilizam o processo de identificação e automatização de rotinas que serão traduzidas para o meio digital. Ou seja, o Lean acaba sendo um pré-requisito para a transformação digital da empresa, tornando-a mais eficiente.
O salto do Lean através da Transformação Digital
Hoje em dia, quando a demanda do cliente é intensamente customizada, há um aumento da complexidade no planejamento. A transparência e compartilhamento de informações atualizadas em tempo real entre clientes, fábrica e a cadeia de fornecedores permite agilidade nas atualizações de reabastecimento e rastreamento dos produtos em tempo real, facilitando a identificação imediata de problemas e sua resolução. Os recursos tecnológicos vieram para auxiliar na gestão desse ambiente complexo e na eliminação mais rápida dos desperdícios, tornando as empresas mais flexíveis e velozes nas tomadas de decisões.
Um exemplo disso é o E-Kanban. Neste sistema são colocados tags com tecnologia UWB (Ultra-wideband) nos paletes ou produtos que podem identificar em tempo real a localização do item com acuracidade de um raio de 30 cm, a quantidade de itens em processo e no inventário. Quaisquer alterações nos parâmetros monitorados geram instantaneamente um alerta em sistema acessível na palma da sua mão através de dispositivos móveis, onde você estiver e no momento da ocorrência. A rapidez da tecnologia propicia a resolução de problemas de forma imediata, algo que antigamente sofria um delay no tempo de comunicação entre a percepção do problema no processo e a ação corretiva, dificultando muitas vezes na identificação do ponto de ocorrência das falhas e estendendo o prazo para a sua resolução em dias ou semanas. E por fim, o mesmo tag também permite o registro da movimentação dos materiais, veículos e pessoas, possibilitando a análise do fluxo de movimentação e rotas de logística interna para a identificação e eliminação de desperdícios sem necessidade de acompanhamento por uma terceira pessoa, seja filmando ou cronometrando.
Apesar de recente, a tecnologia da realidade aumentada também vem sendo utilizada por empresas para melhorar os seus processos. Com o uso de óculos especiais, o colaborador pode visualizar instruções de trabalho, informações dos produtos e pontos de inspeção de qualidade, eliminando o risco de passagem de erros para o processo seguinte. Também são acessíveis informações sobre a localização, quantidade e qual item deve ser retirado do estoque, eliminando o tempo de busca, garantindo o FIFO (First In First Out) e movimentações desnecessárias. Os dados gerados por esses recursos são coletados e, com o uso da inteligência artificial, permitem identificar e analisar a variação de tempos entre os operadores, sugerindo potenciais etapas a serem otimizadas em cada ciclo de atividades. A capacitação de colaboradores também pode aproveitar essa tecnologia, fornecendo um ambiente de realidade virtual com experiência realística das operações e simulando a manutenção da qualidade e produtividade sem gerar riscos à segurança das pessoas e sem utilizar horas máquina.
E lembre-se…
Para que esta transformação digital ocorra de maneira eficiente, recomendo a aplicação de três etapas apresentados por mim no Lean Summit Portugal em 2019:
1. a Transformação Cultural, onde os líderes sejam o exemplo para todos e criem um ambiente seguro que permita falhas para a sua equipe exercitar ciclos rápidos de experimentações, como parte do processo de aprendizado e melhoria contínua;
2. a implementação de uma Transformação Escalável, focando no processo de multiplicação de disseminadores e solucionadores de problemas seguindo o método do Lean Business Practices e;
3. finalmente, a aplicação do que chamo de Lean Digital Intelligence, uma metodologia baseada nos princípios Lean combinadas com técnicas de desenho de arquitetura de soluções de Inteligência Artificial, onde assume-se que os processos já estejam extremamente enxutos, robustos e padronizados, conseguindo-se assim, levar o Lean a um novo patamar.
Ter claro o propósito do uso das novas tecnologias e utilizá-la de acordo com a necessidade, agrega mais valor aos processos, melhora as atividades das pessoas e, principalmente, satisfaz o seu cliente. Em suma, a digitalização e o Lean criam uma sinergia poderosa que maximiza a eficácia dos investimentos realizados pela empresa.
Lando Nishida* – l.nishida@br.honsha.org
*Lando é Diretor Sênior do Honsha.ORG, co-fundador da Lean Academy Portugal, palestrante em eventos de Lean no Brasil e na Europa, formador de gestores em mais de 30 países, certificado em Smart Manufacturing pelo MIT e sócio fundador da PMLean.